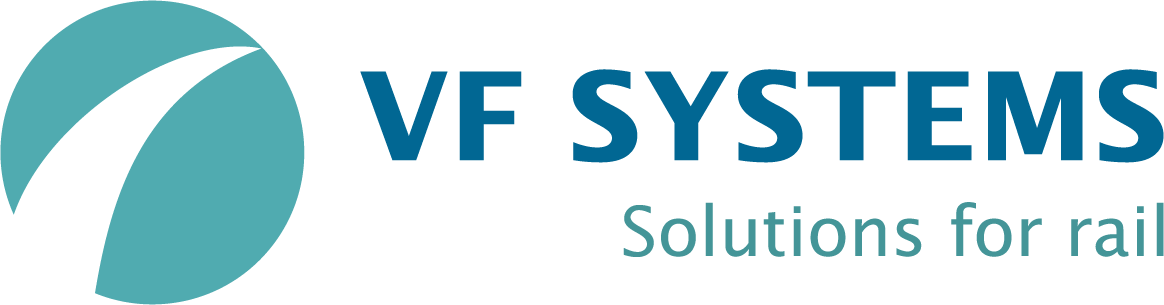
JOINT DE RAIL / Solutions polymériques pour la pose de voie sur dalle béton
RAIL +
Notre entreprise RAIL+ SAS est basée à Romans sur Isère à proximité de l’usine de notre partenaire industriel Covestro Elastomers. Nous développons au sein de notre gamme VF SYSTEMS des solutions polymériques destinées à la pose de rail sur voie béton ainsi que du matériel pour sa mise en œuvre mécanisée.
Nous bénéficions de nombreuses références et nos solutions sont conformes à la plupart des spécifications d’Ingénieries ferroviaires.
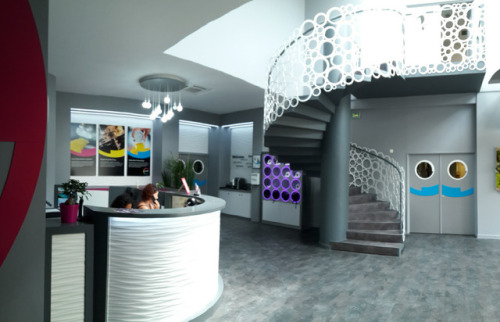
POLYMÈRES APPLIQUÉS AU FERROVIAIRE
Les critères principaux pris en compte dans la mise au point et le dimensionnement de nos procédés polymériques communément appelés « résines » sont :
• Fixation des voies sans ballast : exigences de performance – Norme EN 13481-5 : 2012
La mise en œuvre de polymères pour fixer le rail sur une structure béton permet la transmission des efforts du rail et leur reprise par la surface du béton dans le cadre de deux types de pose de voie :
- La pose directe par appuis discontinus : sur selles de rail.
- La pose continue de type rail noyé : dans une engravure.
Dans tous les cas il faut que la valeur de cohésion superficielle du béton mesurée par un essai de traction directe (NF EN 1542) permette la reprise des efforts transmis par le polymère.
• Atténuation des vibrations : bruit solidien – Norme ISO 2631-2.
Le déplacement des tramways / métros produit un impact dynamique sur de nombreux composants de la structure de la voie, générant des vibrations indésirables qui se propagent à travers le sol pour atteindre les fondations des bâtiments.
Depuis les fondations, les vibrations se propagent à travers la structure et peuvent créer, en plus des désagréments liés aux vibrations, des niveaux de bruit inacceptables pour les occupants du bâtiment.
La circulation du matériel roulant provoque l’émission de vibrations qui, à travers le sol, peuvent être transmises sur de grandes distances. L’origine des vibrations réside dans l’excitation dynamique de la roue sur le rail générée par l’ensemble des charges de roulement, le contact rail-roue ainsi que les imperfections géométriques des roues et des rails.
• Problématique des courants vagabonds (courants de traction) : Norme 50122-2
Les métros et tramways sont alimentés par un courant continu et le retour de courant s’effectue par les rails. Ces rails sont isolés du sol mais une infime partie du courant peut essayer d’emprunter un autre chemin dont les ouvrages métalliques continus non isolés tels que canalisations, câbles, etc…. Les courants circulant dans le sol et issus de systèmes de traction électrique sont appelés « courants vagabonds ». Ces courants vagabonds sont susceptibles d’engendrer des phénomènes de corrosion plus ou moins rapides.
La norme 50122-2 impose donc que le courant de retour de traction se fasse uniquement par la voie avec une résistance longitudinale des rails faible et une voie isolée de la terre.
• Chimie
Les élastomères de polyuréthane thermodurcissables (PUR) que nous proposons sont des polymères de synthèse dont les macromolécules contiennent un certain nombre de fonctions uréthane. Elles sont obtenues par copolymérisation entre un prépolymère et un allongeur de chaîne.
Le prépolymère est obtenu par réaction entre un glycol et un di-isocyanate MDI. Le glycol retenu est le polyéther car il confère à l’élastomère une bonne résistance à l’hydrolyse, une bonne élasticité à basse température, une bonne résilience sur un large intervalle de température et une bonne résistance aux micro-organismes.
L’allongeur de chaîne est soit une amine (composé organique dérivé de l’ammoniac) soit un alcool.
Les polymères à base d’époxyde (époxy par abus de langage) sont eux obtenus par réaction de polymérisation de monomères époxydes (obtenus par oxydation d’un alcène, hydrocarbure insaturé tel l’éthylène) avec un agent de réticulation (appelé durcisseur) : souvent une amine.
Ces polymères requièrent ou non l’application préalable d’un primaire pour adhérer parfaitement sur le support (béton, métal, etc…) préparé.
Ces primaires sont des polymères en phase solvant pour abaisser leur viscosité, imprégner le support et permettre la liaison parfaite entre le support et « la résine » : ce sont les primaires d’accrochage. Ils assurent également la fonction de protection du support préparé (anti corrosion, remontée d’humidité) entre les phases de préparation du support dont ils facilitent le nettoyage et l’application du procédé polymérique : ce sont les primaires d’attente. Les primaires d’attente sont recouverts par les primaires d’accrochage.